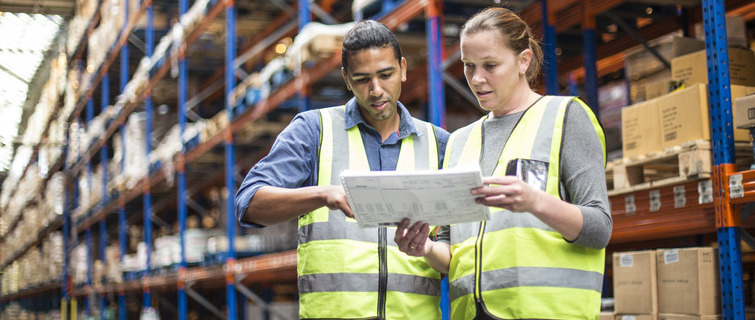
In some ways, their jobs are very different: Simon Myoung performs supply chain due diligence for a consulting company; Faneva Durandisse sources high-end beauty products from around the world; and Albertus Rowan monitors warehouses in Baltimore containing everything from building supplies and industrial cargo to high-tech components and consumer products.
Different industries, different demands, yet essentially the same job: supply chain management, a job category that didn’t even exist by that name until 1982. But in the last 30 years, the field has grown tremendously, both in terms of complexity and the sheer volume of materials that are being transported around the world.
Myoung, Durandisse, and Rowan all elected to earn graduate degrees in the field after they had been practicing it for a few years. That can be a smart decision.
“A master’s degree can help someone get the knowledge of the entire supply chain,” says Linda Dunn, MBA, faculty director of the Master’s in Supply Chain Management program at Georgetown University, which all three attended. “Often, when you start working, you’re in a very narrow component of the supply chain. Maybe you’re working for a freight forwarder, or you’re working in a warehouse, doing warehouse management. But you may not get the full picture of what the supply chain entails.”
The Value of Technical Skills
In addition to a more comprehensive understanding of supply chains and a better grasp of where the field will be headed in the next 10 years or so, the program concentrates on technical skills that many professionals may have missed by working in just one or two areas of the profession.
For example, before enrolling in Georgetown’s program, Myoung had never worked with due diligence reports, the research and analysis typically done on a company prior to a business transaction. However, at Georgetown he took a class specifically in due diligence, whose broad focus showed how the reports could be approached in many different ways.
A month after graduating, Myoung was performing due diligence “deep dives” on companies, suppliers, and transportation modes for the Logistics Management Institute (LMI), where he is a supply chain consultant.
“I didn’t have any knowledge about it previously,” Myoung says, “but I learned in the class, and I could apply those skills to my current job.”
An Expanding Field
When Houston Mason, an instructor in Georgetown’s program, entered the field 30 years ago, more than three-quarters of goods and raw materials were shipped within the United States.
“I tell my students I didn’t have an email account when I first started,” says Mason, Director of Logistics for Canam Steel Corporation near Frederick, Md., noting the amazement of the class. “I started my career working for a trucking company in a management trainee role, and one of my main tasks was fielding calls from customers tracking their shipments, where today shipment tracking is immediately available via multiple ways.”
The field has grown exponentially since Mason started, and its day-to-day procedures have changed considerably. Once largely limited to North America, the vast majority of supply chains now source materials from all over the world. This globalization has expanded the options for consumers and helped keep prices low. Of course, globalization also has a downside, as the public learned in the past few years. Developments as disparate as the war in Ukraine, rising tensions with China, and, perhaps most damaging of all, the COVID-19 pandemic disrupted supply chains around the world and sent companies scrambling for alternatives.
“The fact that things have become more globalized over the years has added to the complexity, added to the risk,” Mason says. As a result, supply chain security and risk management are among the fastest growing segments of this multifaceted field. Other growing specialties include logisticians and operations research analysts, which are expected to grow 28 percent and 23 percent, respectively, between 2021 and 2031—much faster than the average of all occupations, according to the U.S. Bureau of Labor Statistics. Jobs also are plentiful in planning, forecasting, analysis, material management, production, contracting fulfillment, and inventory management.
To succeed in this business, one has to be inquisitive, enjoy problem-solving, attend to details, and like working with people both inside and outside your organization, some of whom are based around the world. And, added Mason, you must be capable of making decisions in real time, when conditions are changing, “when you might not necessarily have 100 percent visibility on things or the whole story.”
“Once I got into the field, the problem-solving aspect was the most interesting,” Mason says. “Even today—30 years on—every day, you solve a problem.